Asphalt batch mixing plant for road construction
Intelligent control, efficient production
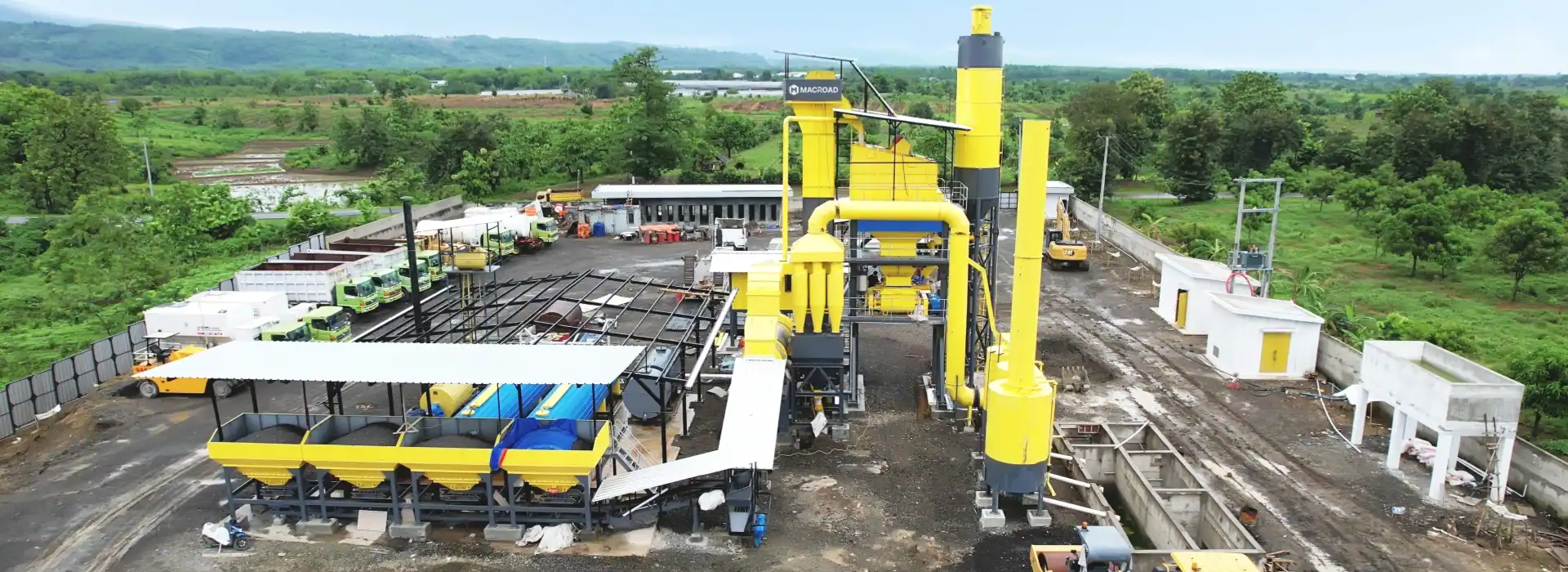
Asphalt batch mix plants are essential equipment for manufacturing high-quality road surface materials. The plant operate in cycles, allowing for accurate weighing and precise dosing of cold aggregates, bitumen, filler, and other additives. It adopts modular design and consists of feeding system, drying system, screening system, mixing system, powder recycling system, finished product storage system, etc. With a quality output, the plant is an ideal mixing system for road maintenance projects, building construction projects, water conservancy construction projects and so on.
Types of asphalt batch plant

Stationary batch asphalt mixing plant
Model: ALQ40~ALQ400
Capacity: 40 t/h ~ 400 t/h
Mixer Capacity: 500kg/batch ~ 5000kg/batch
Highlights: Batch mix, batch mix, precise aggregate batching and weighing; Classic model, wide application, highly cost-effective, best-selling.
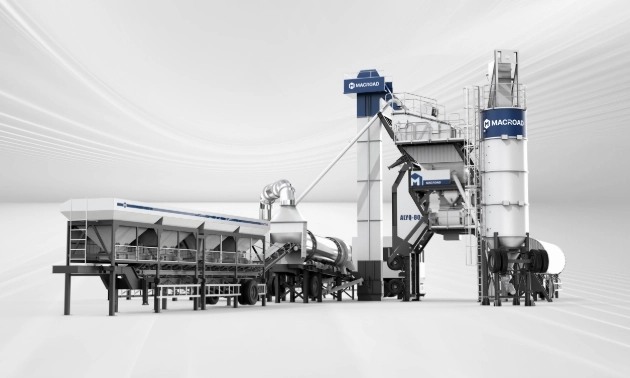
Mobile batch asphalt mixing plant
Model: ALYQ60~ALYQ160
Capacity: 60 t/h ~ 160 t/h
Mixer Capacity: 700kg/batch ~ 2000kg/batch
Highlights: Batch mix, precise screening, accurate weighing, high quality output; easy for installation, fast relocation.

Simple mobile batch asphalt plant
Model: ALYJ10~ALYJ80
Capacity: 10 t/h ~ 80 t/h
Highlights: Batch mixing, less land occupation; precise weighing and screening, low initial cost, highly cost-effective.
Applications of the Asphalt Plant
Asphalt batch mixing plants are core equipment for large-scale infrastructure projects, high-grade road construction and regional material strategic reserves. They are irreplaceable in the construction of highways, hub airports, port heavy-load roads, etc.
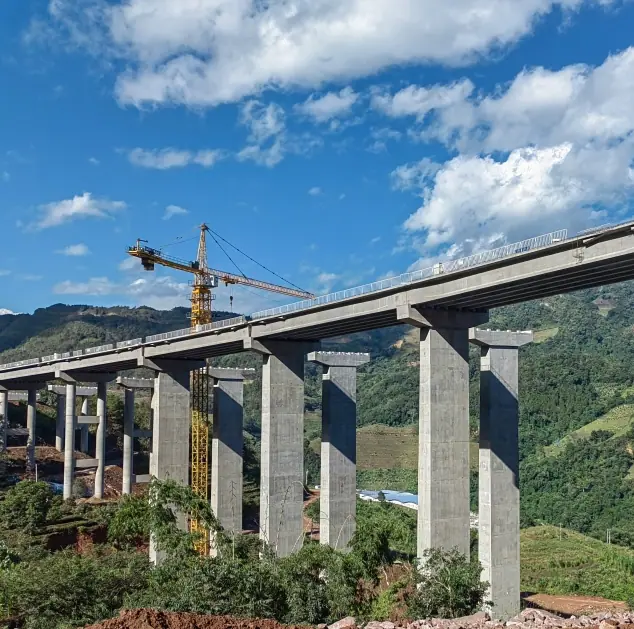
Highway
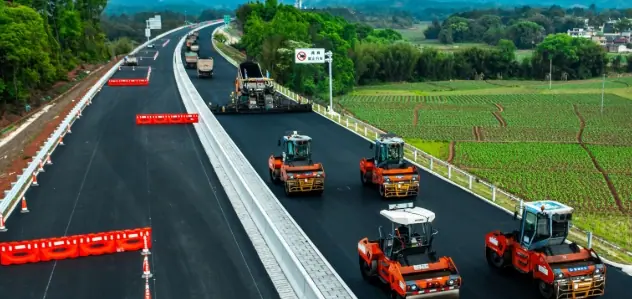
City Expressway

Extraordinary heavy traffic road

Airport Runway
Upgrades of the Main Components
The performance of an asphalt mixing plant hinges on the seamless integration of its core components, each playing a vital role in ensuring productivity and high-quality output. Key components include:
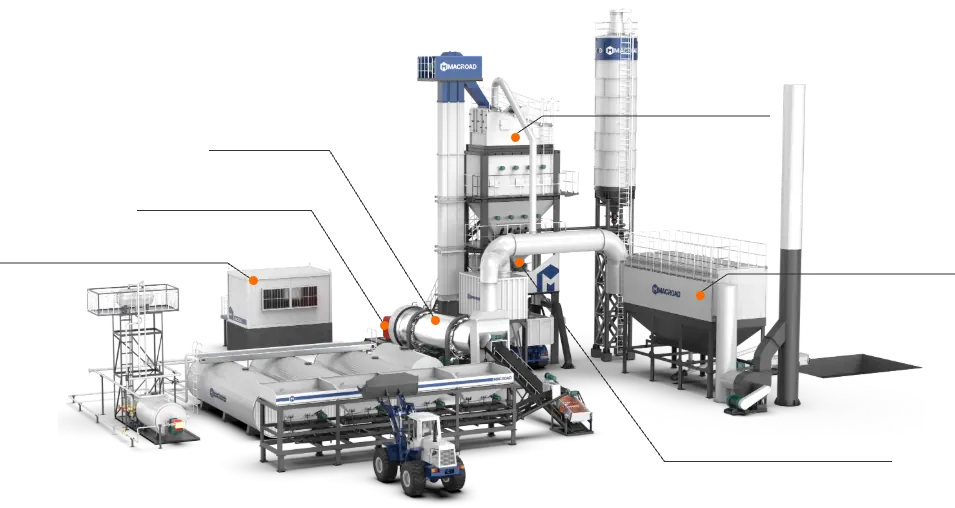
Drying drum
Burner system
Control system
Vibrating screen
Dust filter
Mixing unit
Aggregate batching system
- Main includes: batch hopper, feeding belt, collecting belt, vibrating screen and belt conveyor.
- The hopper capacity is upgraded to 9m³*4, and the belt conveyor is equipped with a pull-rope switch emergency stop device.
Drying system
- Consists of drying cylinders, combustion devices, and oil ignition system components.
- Various fuel options (oil, fine coal, natural gas) to save operating costs.
Screening and mixing system
- Includes vibrating screen, stone, powder, and asphalt weighing, mixer.
- Screen area increased by 30%, improving work efficiency.
Dust Collecting System
- Two collecting levels: cyclone dust filter and bag dust filter.
- Compared with gravity dust removal, cyclone dust removal has better dust removal effect, reduces the load of bag dust collector, and prolongs its life.
Bitumen supply system
- Composed of bitumen tank, bitumen gear pump, pipes, and bitumen spray tube.
- The default fuel for the burner of the thermal oil furnace is diesel, with optional coal and natural gas.
Electrical control system
- Adopts centralized control technology, composed of distribution cabinets, control room, and other small auxiliaries.
- Four operation modes: control cabinet button/touch screen, computer, mobile phone APP.
Global case
We are always a trusted partner in the industry! We have been deeply involved in the field of asphalt mixtures for many years and have provided precise and adaptive solutions for hundreds of road projects around the world; currently including highways, municipal trunk roads, airport runways, port yards and other special scenarios.
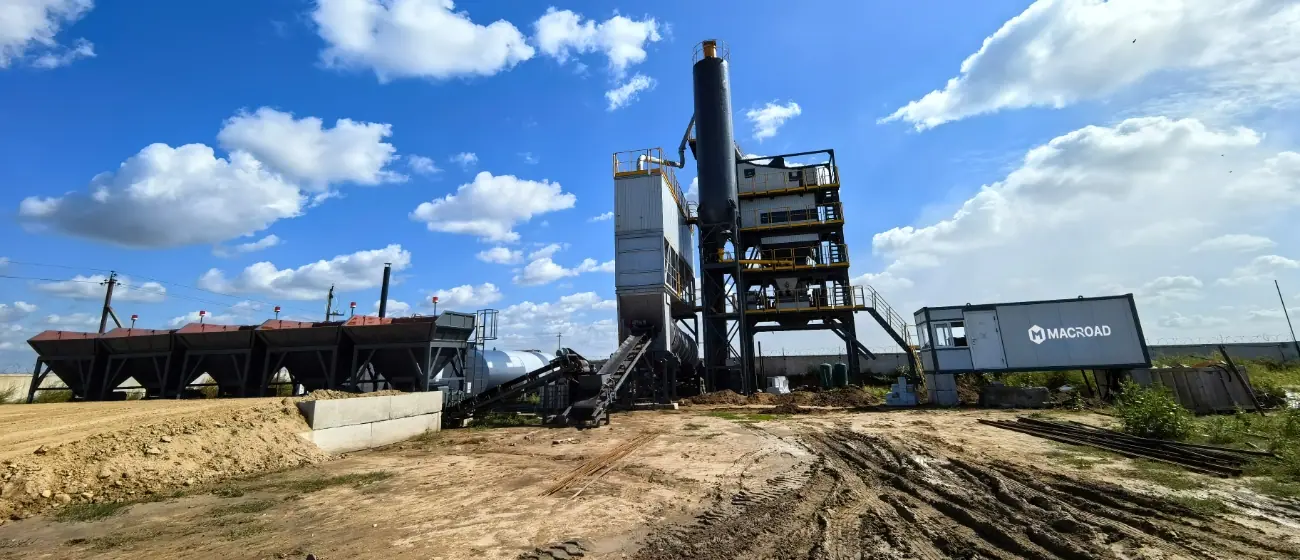
ALQ160 Asphalt batch Mix Plant in Kazakhstan
Pain point: The client wants to produce asphalt for sale,but without experience in the production and installation of equipment
Solution: Engineers to assist in supervision of installation and commissioning on site, as well as for training in production.
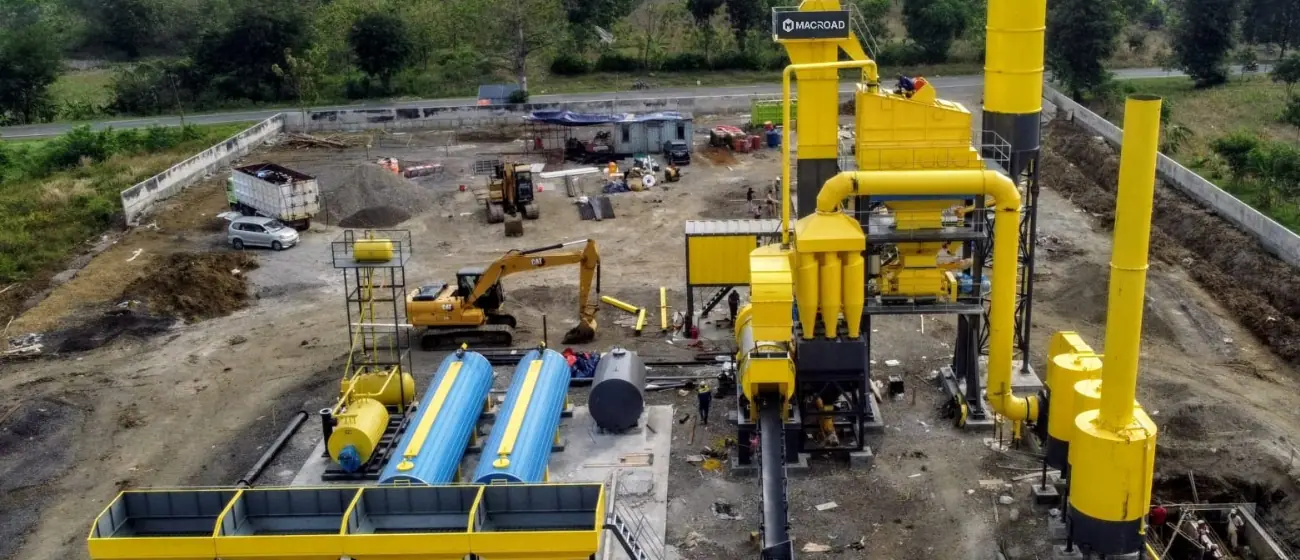
ALQ100 Asphalt Mixing Plant in Indonesia
Pain point: The client wants to achieve cost control and stability of asphalt mixture supply by purchasing an asphalt station
Solution: After the successful operation of Macroad ALQ100 asphalt plant, the customer placed an order for a 100-ton crushing plant again.
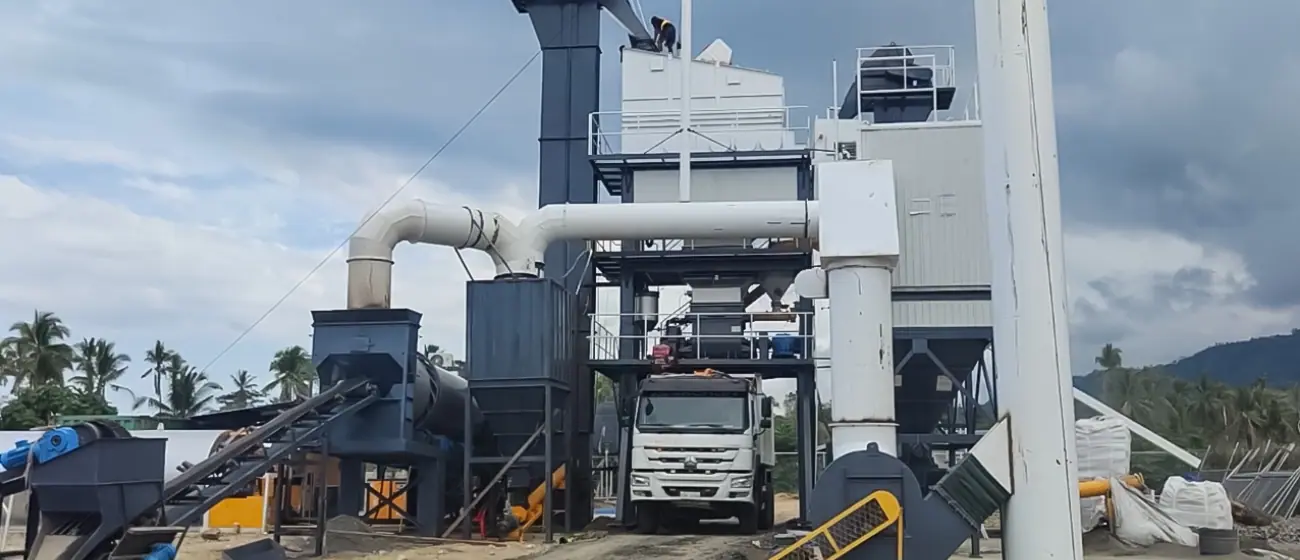
ALQ120+ALT120 Asphalt Mixing Plant for Road Construction in Malaysia
Pain point: Malaysia has a diversified market with strict requirements on infrastructure and requires high reliability solutions.
Solution: Through high-performance equipment and full-process services, Macroad successfully meets the stringent requirements of Malaysian customers for infrastructure projects, and wins customer trust with high-quality support, consolidating market competitiveness.
Our Service
The performance of an asphalt mixing plant hinges on the seamless integration of its core components, each playing a vital role in ensuring productivity and high-quality output. Key components include:
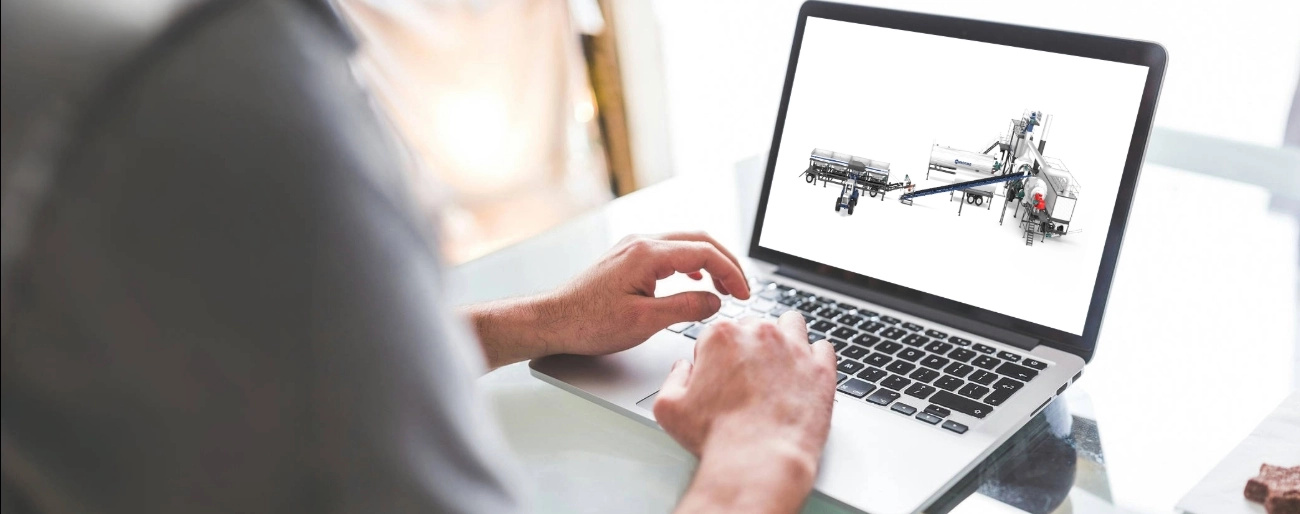
Customized Design Plans
If you are new to the asphalt mixing plant, or need customized plans for your project, we can help you to find the most suitable plan for you. we are aimed to provide solution with reasonable price and perfect service.
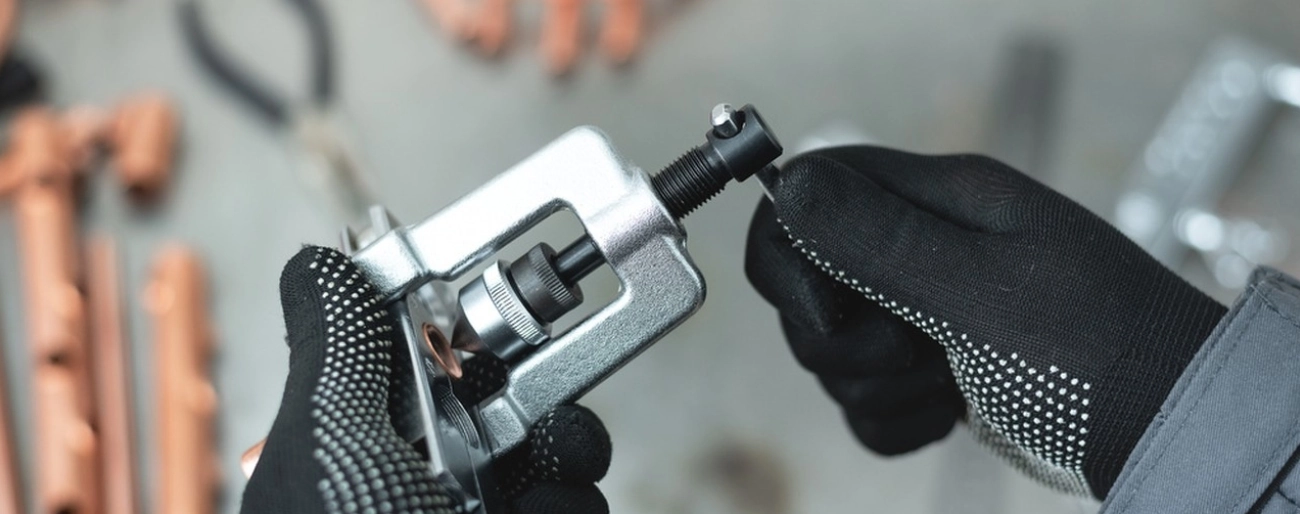
Factory Inspecting Test
Before transportation we will has strict machine inspection to ensure product quality, such as, material supervision, welding inspection, coating inspection, packing inspection, loading inspection, etc.
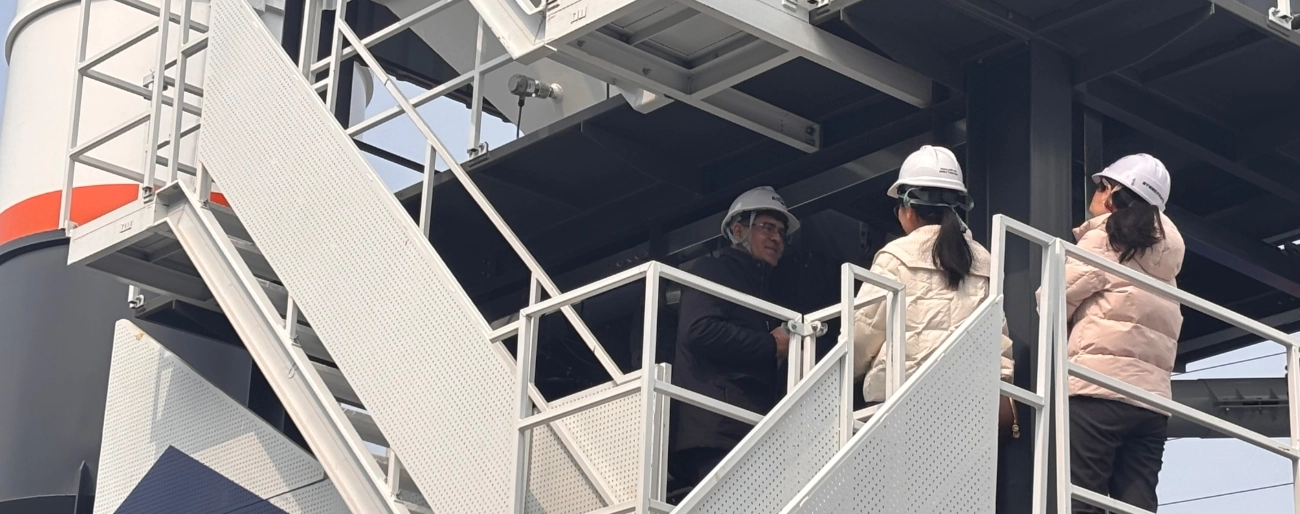
Spare Parts Exchange & Maintenance Service
Providing 12 months warranty. After that we also provide regular maintenance service to you. We will provide you necessary parts and training operator how to exchange them. If we have overseas branches nearby, we will sent our resident engineer to have regular revisit.
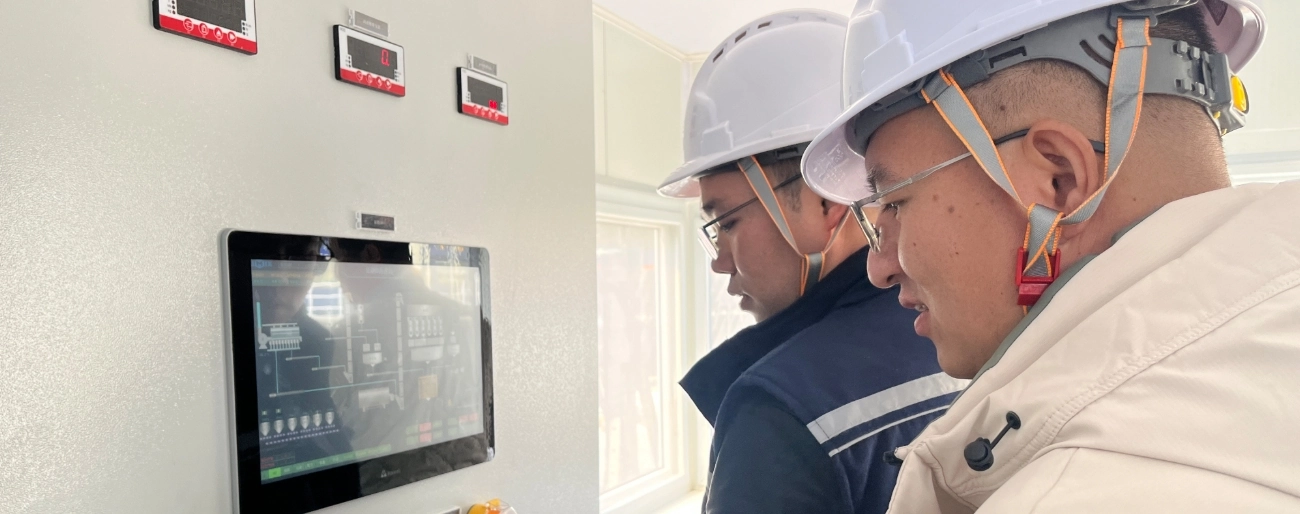
Installation & Commissioning Service
As soon as the machine was shipped to destination, our after-sales engineer will fly to local work-site to help installation, running test and operation training service.
Related Products for Road Construction
The performance of an asphalt mixing plant hinges on the seamless integration of its core components, each playing a vital role in ensuring productivity and high-quality output. Key components include: