Patented process chain drives the full cycle sustainable development of road and bridge projects
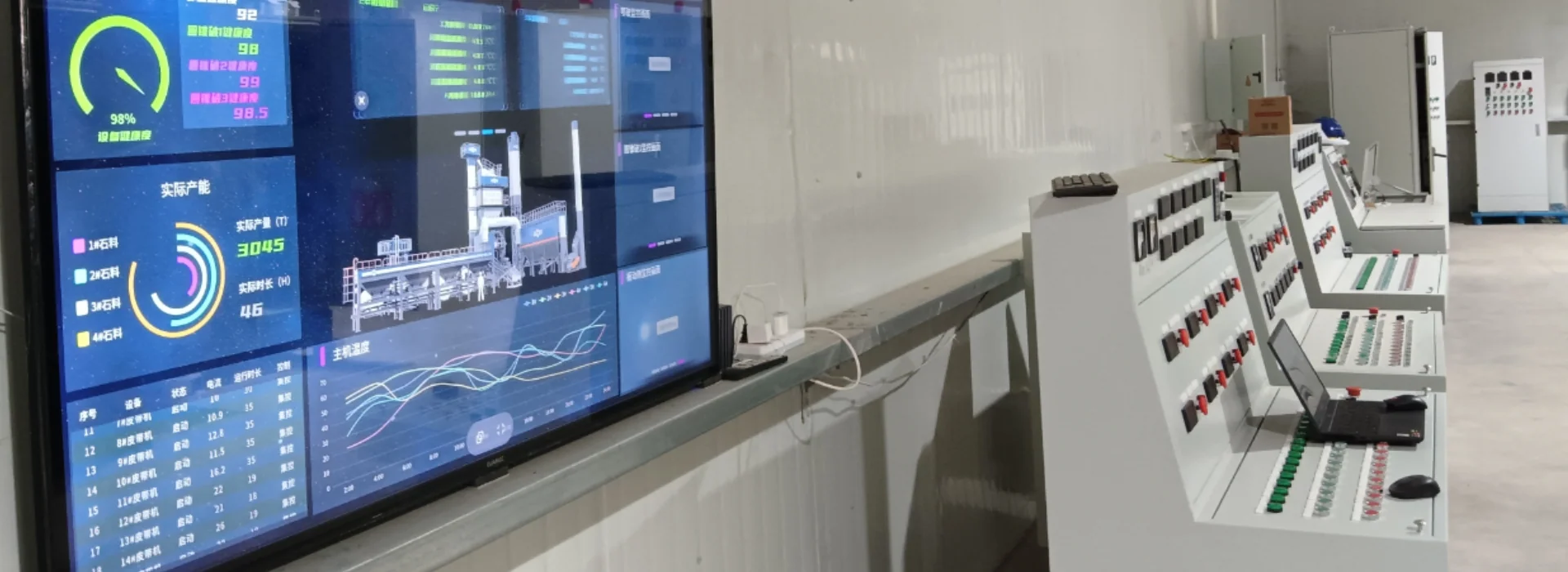
The Latest in Asphalt Production Technology
By integrating the advanced asphalt production technology and intelligent construction process system with independent patents, we provide full life cycle technical support for modern transportation road and bridge projects, and promote the upgrading of road infrastructure towards digital production and low-carbon construction.
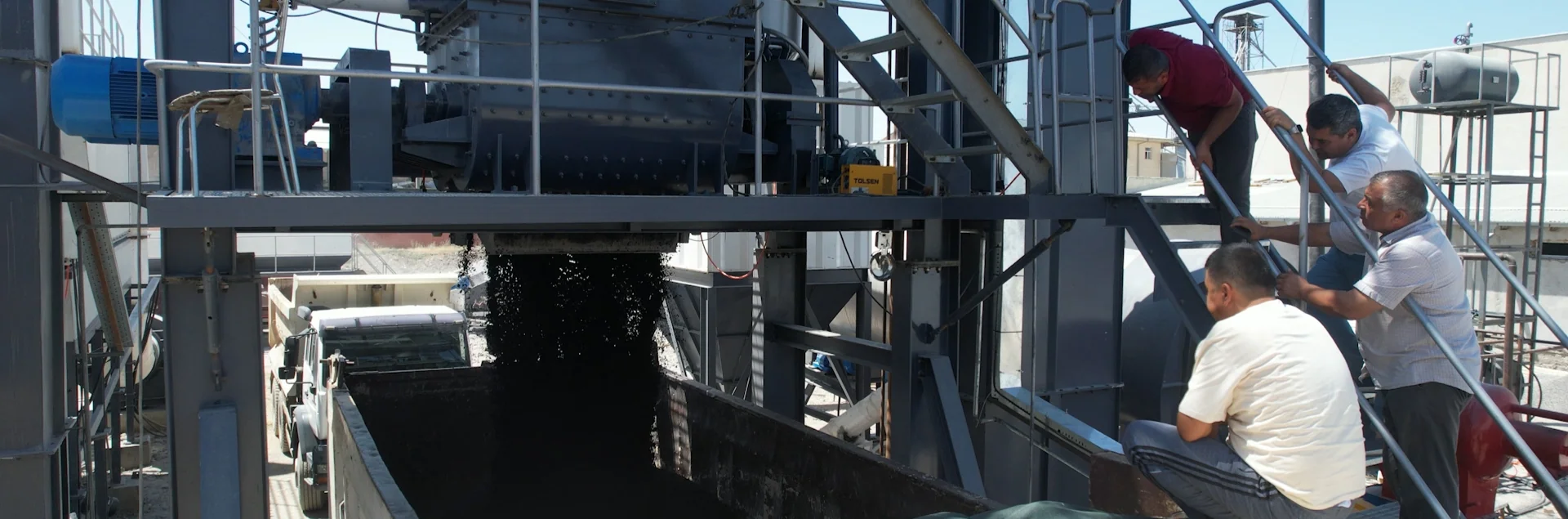
100 % efficient, sustainable & profitable
Intelligent technology: → Improve production efficiency by 28%
Environmental protection technology → 100% compliance with environmental protection acceptance
Recycled asphalt technology → Extend the road life by 15%
Modular design: → Shorten the construction period by 60%
Energy-saving technology: → Save 25% of fuel costs
Details of our Core Technology
With the upgrading of the infrastructure industry’s demand for efficiency, environmental protection and intelligence, modern asphalt mixing plants have evolved from traditional mechanical devices to “green smart factories” that integrate multiple cutting-edge technologies. We deeply analyze the key technology implementation paths and their core value to customers from five dimensions: environmental protection, intelligence, regeneration, modularization, and energy saving.
Intelligent technology: data-driven unmanned production
1. AI automatic proportioning system
- Multi-source data fusion: Aggregate composition (through XRF spectral analysis), asphalt penetration (online viscometer), ambient temperature and humidity are collected in real time; Combined with historical production data (such as grading curve, compaction degree) to train the neural network model.
- Dynamic optimization algorithm: Input the target Marshall index (stability, flow value), AI outputs the optimal solution for aggregate grading, oil-stone ratio, and RAP dosage; Automatically fine-tune parameters according to sensor feedback (such as mixing temperature) during production.
- Customer benefits: The fluctuation of mixed material quality is reduced by 70%, reducing the rework loss caused by mis-proportioning.
2. Remote operation and maintenance platform
- IoT architecture: Equipment of vibration and temperature sensors on key equipment components (motors, bearings); 5G/4G modules upload data to the cloud;
- Fault prediction and diagnosis: Based on the digital twin model, compare real-time data with the standard operation curve; Pre-warning of potential faults (such as triggering an alarm when bearing wear is greater than 0.2mm).
- Customer benefits: Engineers remotely guide to eliminate 90% of common faults, and the maintenance response time is shortened from 24 hours to 2 hours.
Environmental protection technology
1. High-efficiency dust removal system (cyclone bag + bag dust removal)
- Multi-stage filtration design: Primary cyclone dust removal: remove large particles of dust (particle size > 50μm) through a cyclone separator;
- Bag dust removal: use high temperature resistant (≤200℃) coated filter bags with a filtration accuracy of 1μm to intercept fine particles;
- Intelligent dust cleaning control: according to the pressure difference sensor data, automatically trigger the pulse spray system to clean the filter bag to maintain a dust removal efficiency of ≥99.5%.
- Customer benefits: Dust emission ≤20mg/m³, dust in the factory area is visibly reduced, and environmental protection tests are easily passed.
2. Asphalt flue gas purification (activated carbon/low temperature plasma)
- Activated carbon adsorption tower: The flue gas enters the adsorption layer after being cooled to 40-60℃;The honeycomb activated carbon adsorbs harmful substances such as benzopyrene, and can be desorbed and regenerated at high temperature after saturation.
- Low temperature plasma technology: The high-voltage electric field ionizes the flue gas to produce highly active free radicals (such as OH);Free radicals decompose VOCs into CO₂ and H₂O, without secondary pollution.
- Customer benefits: The odor in the factory area is reduced by 80%, reducing residents’ complaints and employee health risks.
3. Recycled material addition technology (RAP ratio 30%-50%)
- Old material crushing and screening system: The milling material is crushed to ≤25mm by a double-shaft crusher;Multi-layer vibrating screen classification (0-5mm, 5-10mm, 10-25mm) to remove impurities.
4. Precise metering and blending
- RAP silo is equipped with weighing sensor and infrared moisture meter;The ratio of new material to old material is automatically adjusted according to the formula, with an error of ≤0.5%.
- Customer benefits: The cost of each ton of mixed material is reduced by 15-30 yuan, and the annual savings exceed one million yuan (calculated based on 100,000 tons/year).
Recycled Asphalt Technology
1. Warm mix asphalt (WMA)
- Foamed asphalt technology: Asphalt is pumped into the foaming chamber and injected with 2%-5% water;It expands instantly at high temperature (160-180℃), the volume increases by 10-20 times, and the aggregate is wrapped more evenly.
- Addition of organic viscosity reducer: Add fatty acid derivatives (such as Evotherm) to reduce asphalt viscosity;The production temperature is reduced from 160℃ to 120℃, and fuel consumption is reduced by 25%.
- Customer benefits: 3-5kg CO₂ emissions are reduced per ton of mixture, which meets the requirements of carbon trading policies.
2. High proportion of recycled material mixing (RAP>50%)
- Double drum hot regeneration technology: The outer drum heats the new aggregate to 200℃, and the inner drum preheats the RAP to 130℃ (to avoid aging of old asphalt);
- The new and old materials are mixed in the mixing area, and the fusion degree of new and old asphalt is increased to 95%.
- Precise spraying of regeneration agent: According to the degree of RAP aging (analyzed by fluorescence microscope), regeneration agent (such as aromatic oil) is added dynamically;Restore the ductility of old asphalt to ≥40cm (25℃).
- Customer benefits: When the RAP utilization rate reaches 60%, the material cost is reduced by 40%, and a subsidy of 30-50 yuan per ton is obtained from the local government.
Modular design: Rapid Response Engineering Adaptation
1. Container structure
- Standardized module division: The drying drum, mixing cylinder, and control system are packaged into independent containers (size: 12.2m×2.4m×2.9m);The modules are connected by flanges + hydraulic locks, and the bolt tightening time takes less than 4 hours.
- Foundation-free installation: Adopt hydraulic leg leveling system to adapt to complex terrain such as sand, mud, etc.;The installation cycle of the whole station is shortened from 30 days to 7 days.
- Customer benefits: The cost of site construction in remote areas is reduced by 50%, and the engineering flexibility is greatly improved.
2. Plug-and-play control unit
- Pre-installed embedded system: The controller is preloaded with standardized programs;Automatically identify the device topology after inserting the fiber optic interface.
- OTA remote upgrade: Download new formulas or algorithms through encrypted channels;Software iteration can be completed without downtime.
- Customer benefits: Technician training time is compressed from 1 month to 3 days, and equipment upgrade efficiency is increased by 90%.
Energy-saving technology: “squeezing” value from exhaust gas
Burner waste heat recovery system
- Heat pipe heat exchanger: The exhaust gas (250-300℃) flows through the evaporation section of the heat pipe, and the heat is transferred to the condensation section;Preheating cold aggregate from 20℃ to 80℃ reduces drying energy consumption.
- Closed-loop control: Temperature sensors adjust exhaust gas flow in real time;Ensure aggregate preheating is stable to avoid overheating and coking.
- Customer benefits: 1.2-1.8 liters of diesel are saved per ton of mixture, and annual fuel cost savings exceed 500,000 yuan (calculated based on an annual output of 100,000 tons).
Patent certification
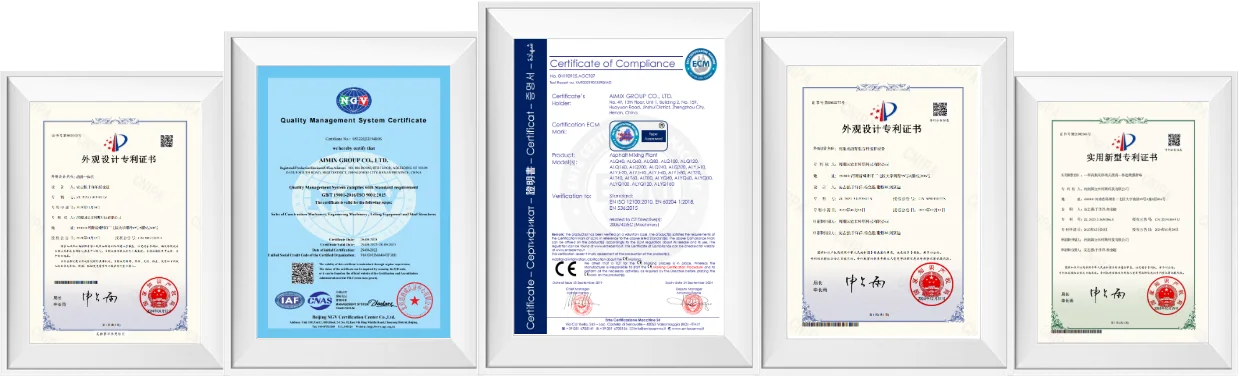
Utility model patent for mobile drum mixer
Asphalt station pipeline expansion technology
Design patent certificate
Patent certificate for high-integrated asphalt mixture mixing equipment
Quality Control System
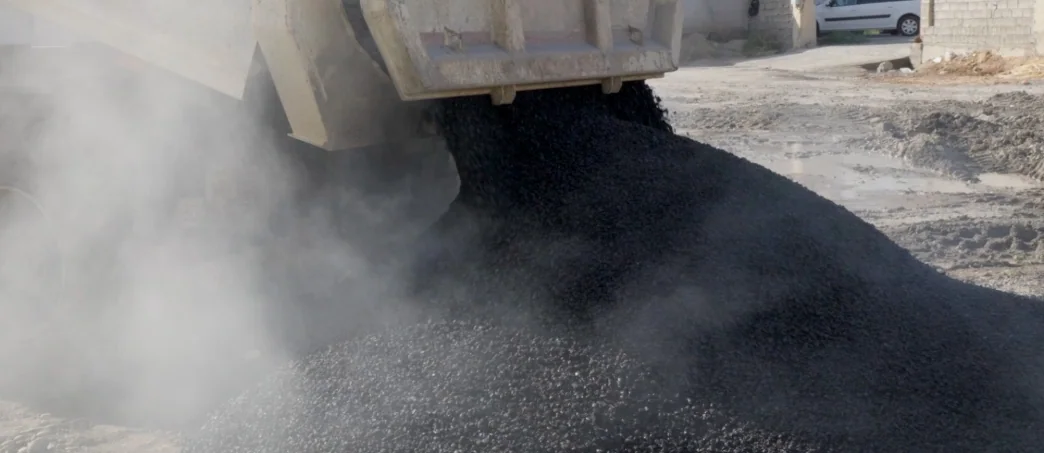
On the technical level
we introduce the international cutting-edge asphalt production process, equipped with a professional and experienced technical team, and accurately control the production process throughout the process to ensure that the performance of each batch of asphalt products can meet the high standards of the industry. From the beginning of raw material procurement, we have established a strict screening mechanism, worked closely with high-quality suppliers, and conducted detailed inspections on each batch of raw materials to prevent unqualified raw materials from entering the production process.
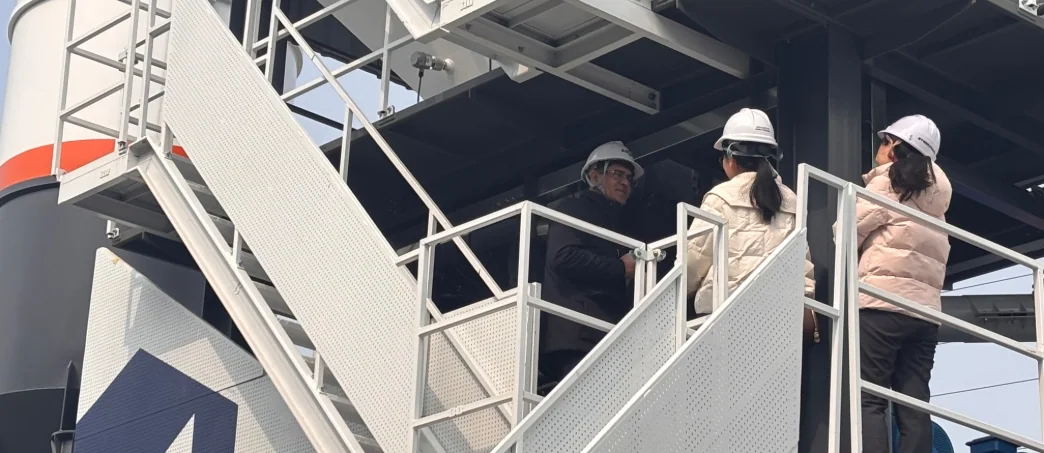
Customization Solutions
we have established a complete and efficient internal management process based on internationally accepted quality management system standards. From production planning, equipment operation and maintenance to personnel training and performance appraisal, there are detailed and scientific rules and regulations. Through regular internal audits and management reviews, we continuously optimize the management system to ensure smooth and stable production operations.

In terms of testing
testing capabilities are a powerful testimony to our strength. The station is equipped with an advanced laboratory equipped with complete testing equipment, which can accurately test the key indicators of asphalt products such as penetration, softening point, and elongation.